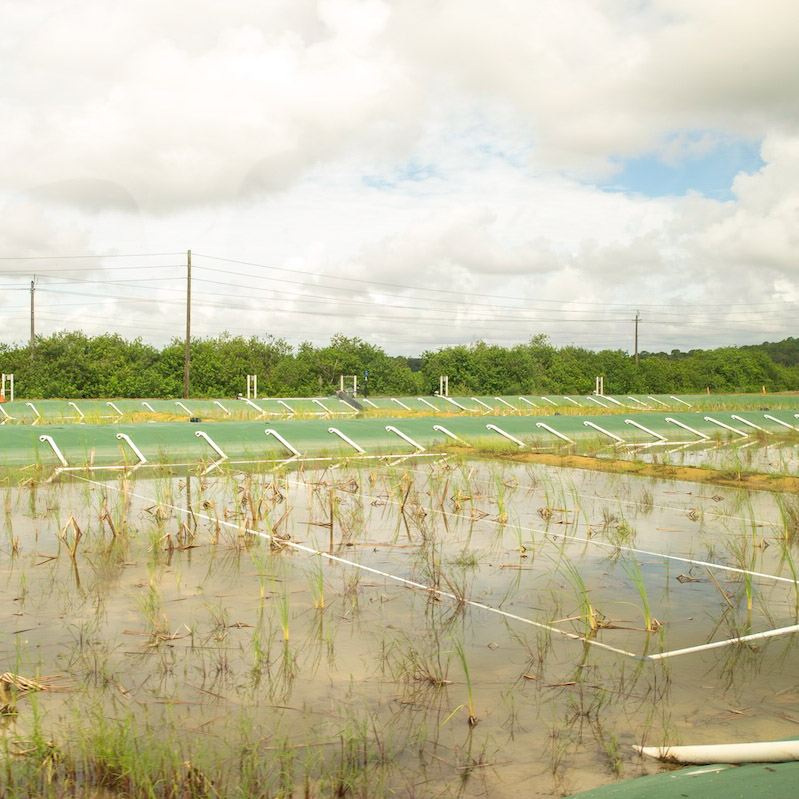
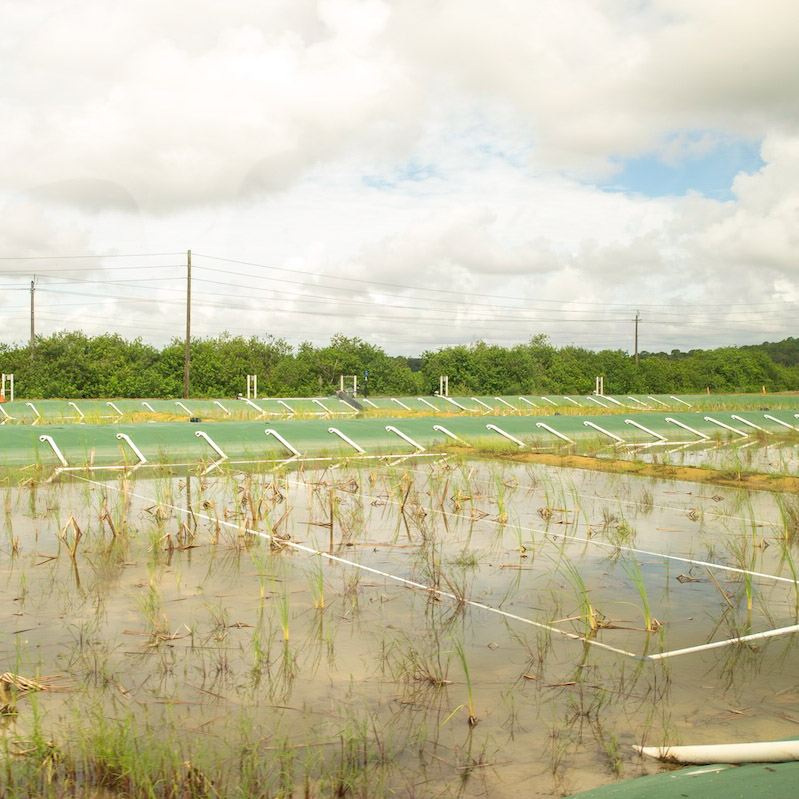
Research Terms
Engineering Environmental Engineering Waste Management Hazardous Wastes Solid Waste Landfills Recycling
2012
Kim, H., Townsend, T. (2012) “Wet landfill decomposition rate determination using methane yield results for excavated waste samples.” Waste Management. 32(7):1427-433. doi:10.1016/j.wasman.2012.03.017.
Singh, S., Townsend, T., Boyer, T. (2012). “Evaluation of coagulation (FeCl3) and anion exchange (MIEX) for stabilized landfill leachate treatment and high-pressure membrane pretreatment.” Separation and Purification Technology. 96:98-106. doi:10.1016/j.seppur.2012.05.014.
Xu, Q., Tolaymat, T., Townsend, T. (2012) “Impact of Pressurized Liquids Addition on Landfill Slope Stability.” Journal of Geotechnical and Geoenvironmental Engineering, ASCE.” 138(4):472-480. doi:10.1061/(ASCE)GT.1943-5606.0000609.
Wang, Y., Sikora, S., Kim, H. Dubey, B., Townend, T. (2012) “Mobilization of iron and arsenic from soil by construction and demolition debris landfill leachate.” Waste Management. 32(5): 925-932. doi:10.1016/j.wasman.2011.11.016.
Xu, Q., Kim, H., Jain, P., Townsend, T. (2012) “Hydrologic evaluation of landfill performance (HELP) modeling in bioreactor landfill design and permitting.” Journal of Material Cycles and Waste Management. 14(1):38-46. doi:10.1007/s10163-011-0035-8.
Larson, J., Kumar, S., Gale, A., Jain, P., Townsend, T. (2012) “A field study to estimate the vertical air permeability of compacted MSW using a barometric pumping analytical model.” Waste Management and Research. 30(3): 276-284. doi:10.1177/0734242X11424592.
Singh, S., Townsend, T., Mazyck, D., Boyer, T. (2012) “Equilibrium and intra-particle diffusion of stabilized landfill leachate onto micro- and meso-porous activated carbon.”Water Research. 46(2):491-499. doi:10.1016/j.watres.2011.11.007.
Timmons, J., Cho, Y., Townsend, T., Berge, N., Reinhart, D. (2012) “Total earth pressure for measuring loads in a municipal solid waste landfill.” Geotechnical and Geological Engineering. 30(1):95-105. doi:10.1007/s10706-011-9452-7.
Kim, H., Jang, Y-C., Townsend, T. (2011) “The behavior and long-term fate of metals in simulated landfill bioreactors under aerobic and anaerobic conditions.” Journal of Hazardous Materials. 194:369-377. doi:10.1016/j.jhazmat.2011.07.119.
Townsend, T. (2011) “Environmental issues and management strategies for waste electronic and electrical equipment.” Journal of the Air and Waste Management Association. 61:587-61.
Kadambala, R., Townsend, T., Jain, P., Singh, K. (2011) “Temporal and spatial pore water pressure distribution surrounding a vertical landfill leachate recirculation well.”International Journal of Environmental Research and Public Health. 8(5):1692-1706.doi:10.3390/ijerph8051692.
Boyer, T., Graf, K., Comstock, S., Townsend, T. (2011) “Magnetic ion exchange treatment of stabilized landfill leachate.” Chemosphere. 83(9):1220-1227.doi:10.1016/j.chemosphere.2011.03.040.
Xu, Q., Townsend, T., Bitton, G. (2011).“Inhibition of Hydrogen Sulfide Generation from Disposed Gypsum Drywall Using Chemical Inhibitors.” Journal of Hazardous Materials. 191(1-3):204-211. doi:10.1016/j.jhazmat.2011.04.063.
Ko, J., Musson, S., Townsend, T. (2011). “Removal of trichloroethylene from soil using the hydration of calcium oxide.” Journal of Environmental Management. 92(7):1767-1773. doi:10.1016/j.jenvman.2011.02.004.
Wise, W., Townsend, T. (2011) “One-dimensional gas flow models for municipal solid waste landfills: Cylindrical and spherical symmetries.” Journal of Environmental Engineering, ASCE. 137:514-516. doi:10.1061/(ASCE)EE.1943-7870.0000342.
Hasan, A., Schindler, J., Solo-Gabriele, H., Townsend, T. (2011). “Online sorting of recovered wood by automated XRF-technology. Part I: Detection of preservative treated wood waste.” Waste Management. 31(4): 688-694. doi:10.1016/j.wasman.2010.11.010
Hasan, A., Solo-Gabriele, H., Townsend, T. (2011). “Online sorting of recovered wood by automated XRF-technology. Part II: Sorting efficiencies.” Waste Management. 31(4): 695-704. doi:10.1016/j.wasman.2010.10.024.
Cho, Y., Ko, J., Chi, L., Townsend, T. (2011) “Food Waste Impact on Municipal Solid Waste Angle of Internal Friction.” Waste Management. 31:26-32. doi:10.1016/j.wasman.2010.07.018.
This Portland cement manufacturing system reliably integrates the bottom ash remaining after municipal solid waste incineration as a component in the raw kiln feed. The world produces more than 2 billion metric tons of municipal solid waste each year. In the United States, most solid waste is added to landfills. In some instances, solid waste is incinerated instead; while incineration greatly reduces waste volume, 20-35 percent of its weight remains as bottom ash. Recycling the bottom ash as material for cement production is attainable and would be a profitable means of reducing global waste. Replacing even up to 5 percent of Portland cement raw materials with incineration ash would significantly offset costs of global cement production and waste management.
Researchers at the University of Florida have developed a procedure for creating Portland cement that incorporates the world’s abundant supply of waste incineration ash as an input material. The process is an economically viable way to recycle bottom ash that reduces the environmental impact of both municipal solid waste incineration and cement manufacturing.
A system for manufacturing Portland cement, which incorporates ash from municipal solid waste incineration as a raw ingredient in the kiln feed.
This Portland cement manufacturing system enables use of municipal solid waste bottom ash in the cement kiln feed. Bottom ash is a safer alternative to other potential cement kiln ingredients such as fly ash, which has detrimental metal leaching properties. The system can replace up to 5 percent of the raw kiln feed with recycled bottom ash. The kiln feed containing the bottom ash forms ash-amended clinker, which when ground mixes to prepare cement products comparable to normal Portland cement products.
This waste treatment system removes per-fluorinated compounds from landfill leachate before they can enter the ground water. Landfill leachate is the liquid that forms when rainwater percolates through landfills and collects toxic substances. Compounds like perfluorooctanoic acid (PFOA) and other per- and poly-fluoroalkyl substances (PFAS) do not breakdown in natural environments and are documented hazards to human health. These compounds have been associated with diseases including kidney and testicular cancer, increased cholesterol, reproductive and developmental damage, and reduced effectiveness of vaccines. Federal regulations require leachate removal in the more than 1900 municipal solid waste landfills in the United States, necessitating development of systems for efficiently removing hazardous PFAS and PFOA compounds.
Researchers at the University of Florida have developed a waste treatment system that removes perfluoroalkyl materials from landfill leachate. The inexpensive process concentrates the stream containing the harmful chemicals for more efficient high-energy destructive PFAS treatment.
Waste treatment system that isolates hazardous per-fluorinated materials from landfill leachate before they enter the ground water
This waste treatment process uses aeration to induce foaming that separates perfluoroalkyl substances from a volume of landfill leachate. Isolating the PFAS compounds into a coalesced foam and reducing that foam into a concentrated liquid allows efficient treatment of the compounds using high-energy destructive processes such as sonication, chemical oxidation, electron beam, and plasma treatments. The waste treatment system cleans municipal solid waste landfill leachate of PFAS and PFOA.
This highly efficient plasma arc reactor eliminates fuel-borne CO2 emissions and facilitates recycled waste use in manufacturing traditional portland cement. The concrete and cement industry is expected to grow 8 percent by 2023 . Cement plants worldwide utilize a rotatory kiln to generate the clinker used to produce portland cement. However, these kilns negatively contribute to total greenhouse gas emissions and cannot perform at exceedingly high temperatures, limiting the efficiency of cement manufacturing.
Researchers at the University of Florida have developed a high-temperature plasma arc reactor capable of producing the main ingredient of portland cement, clinker, in a highly controlled environment. This reactor avoids the clinker contamination possible with rotary kilns, enables use of recycled waste byproducts in cement manufacturing, and has a less harmful impact on the environment.
A high-temperature plasma arc reactor for cement clinker production that reduces the carbon footprint of cement manufacturing
This reactor aims to optimize and refine cement clinker production by employing high temperatures and a controlled environment. The reactor utilizes a plasma torch to perform the thermal treatment and can fully automate temperature up to 3,000 degrees Celsius, which is twice the temperature produced by a rotary kiln. It also generates the heat without traditional fuel sources to eliminate fuel-borne C02 emissions. After manufacturing clinker, a quantitative X-ray diffraction uses a Rietveld refinement technique to analyze its mineralogical compositions for optimal cement phases.
This filtering and curing treatment of waste to energy bottom ash results in a beneficial composite that can be mixed with cement to form environmentally safe concrete. Waste to energy bottom ash or incinerator ash is a portion of the non-combustible residue that remains after waste combustion. Municipal waste combustion generates 7-8 million tons of waste in the United States annually and, because it has the potential to leach concentrations of heavy metals, it currently requires disposal in secure landfills. The construction, permitting, compliance and operating costs of a landfill are significant; recycling bottom ash for beneficial use instead of storing it in a landfill would be a significant cost savings for ash generators. Researchers at the University of Florida have developed a filtering and curing treatment that immobilizes contaminants in the bottom ash and creates a properly graded and usable aggregate product for use in asphalt and concrete or as a roadway base.
Immobilizes contaminants from waste to energy bottom ash allowing use as a construction aggregate
Bottom ash from municipal waste is processed through physical processes to use as an aggregate for a road base, or in Portland cement concrete and hot mix asphalt. The bottom ash moves through gradation screenings to remove metals, elements, alloys and other contaminants. The ash is then cured by selective exposure to water and atmospheric CO2, effectively lowering the pH of the ash and creating an environment that washes heavy metals and trace elements from the ash. The resulting composite has few negative health and environmental effects while maintaining similar structural properties to alternative composites.