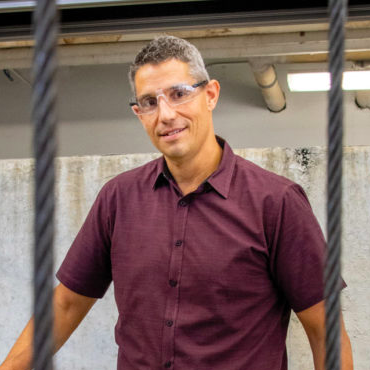
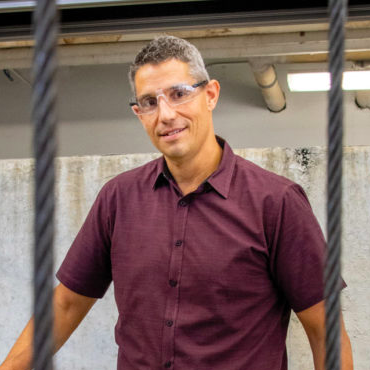
Research Terms
Engineering Construction Engineering Concrete Structures Building Materials
Industries
Advanced Materials & Products Green Buildings
This Portland cement manufacturing system reliably integrates the bottom ash remaining after municipal solid waste incineration as a component in the raw kiln feed. The world produces more than 2 billion metric tons of municipal solid waste each year. In the United States, most solid waste is added to landfills. In some instances, solid waste is incinerated instead; while incineration greatly reduces waste volume, 20-35 percent of its weight remains as bottom ash. Recycling the bottom ash as material for cement production is attainable and would be a profitable means of reducing global waste. Replacing even up to 5 percent of Portland cement raw materials with incineration ash would significantly offset costs of global cement production and waste management.
Researchers at the University of Florida have developed a procedure for creating Portland cement that incorporates the world’s abundant supply of waste incineration ash as an input material. The process is an economically viable way to recycle bottom ash that reduces the environmental impact of both municipal solid waste incineration and cement manufacturing.
A system for manufacturing Portland cement, which incorporates ash from municipal solid waste incineration as a raw ingredient in the kiln feed.
This Portland cement manufacturing system enables use of municipal solid waste bottom ash in the cement kiln feed. Bottom ash is a safer alternative to other potential cement kiln ingredients such as fly ash, which has detrimental metal leaching properties. The system can replace up to 5 percent of the raw kiln feed with recycled bottom ash. The kiln feed containing the bottom ash forms ash-amended clinker, which when ground mixes to prepare cement products comparable to normal Portland cement products.
This concrete formulation and or cementitious coating contains boron to protect against radiation-induced volumetric expansion. Many facilities use concrete to shield against radiation, such as nuclear power plants or radiological medical facilities. The global nuclear power plant and equipment market is projected to reach $4.9 billion by 2025. Concrete is prone to degradation in certain environments, a result of chemical reactions between alkalis and other materials in the concrete mixture. Some concrete formulations use boron aggregates to make concrete structures resistant to radiation, but the inherently uneven aggregate dispersion leaves surfaces exposed and the structure susceptible to radiation-induced volumetric expansion (RIVE), which may lead to further degradation due to alkali silica reactivity (ASR) of aggregates that are otherwise non-reactive.
Researchers at the University of Florida have developed a formulation for concrete or concrete coatings to help prevent degradation due to radiation. The formulation utilizes boron compounds that decay into lithium, which can suppress the expansive chemical reactions that cause degradation.
Boron-containing compounds in concrete and cementitious coatings to protect against radiation damage and increase concrete’s durability and service-life
Concrete formulations often use lithium salts to reduce the potential for alkali silica reactivity degradation and boron aggregates to provide neutron shielding. This formulation includes boron-containing compounds, such as fine powders, liquid solutions, or liquid suspensions, in the mixture of cementitious materials. When exposed to neutron radiation, the boron transforms in situ through radioactive decay into lithium. The formulation also contains hydrogenous compounds to aid in providing shielding from thermal neutrons as well as the thermalization of fast neutrons for additional shielding benefits. This protects the radiation-damaged aggregates and prevents alkali-silica reactions due to radiation-induced volumetric expansion. A shielding coating for concrete using this formulation can be applied directly to a surface prepared for bonding or mechanically as pre-formed panels that secure onto an existing structure. The protective coating can be applied in just days, reducing facility downtime and installation costs while allowing for regular inspection and replacement.
This magnetic inductive sensing device confirms that reinforcement in concrete structures is aligned correctly to prevent catastrophic failure. The electromagnetic system detects the density and orientation of metallic fibers in Ultra-High-Performance Concrete (UHPC) as well as rebar and other ferromagnetic substance in concrete. Civil engineering projects, new buildings, and pre-fabricated structures increasingly use UHPC due to its strength, but it suffers from inconsistent distribution of the metal fibers in it. The collapse of the Surfside condominium in South Florida in 2021 highlights the need for a better system for inspecting concrete structures. With the global construction industry expected to reach USD $16.6 trillion by 2025, it is increasingly important to evaluate the safety of structures.
Researchers at the University of Florida have developed a device that uses magnetic inductance to detect whether the metal fibers are clumped together or evenly distributed, aiding in quality control inspections of ultra-high performance concrete and other concrete. This work enables construction and inspection companies to monitor the quality of their UHPC slabs or prefabs on site.
Quality control and inspection of UHPC and other concrete structures such as bridges, parking garages, buildings, and more
This technology uses an inductive sensor to characterize the density and orientation of ferromagnetic materials in ultra-high-performance concrete. It works by magnetic induction, where a changing magnetic field causes an electric current in the material being studied, and the changing electric current causes another magnetic field in turn. The sensor is connected to a data acquisition device which records the location of each area of strong magnetic inductance.
This highly efficient plasma arc reactor eliminates fuel-borne CO2 emissions and facilitates recycled waste use in manufacturing traditional portland cement. The concrete and cement industry is expected to grow 8 percent by 2023 . Cement plants worldwide utilize a rotatory kiln to generate the clinker used to produce portland cement. However, these kilns negatively contribute to total greenhouse gas emissions and cannot perform at exceedingly high temperatures, limiting the efficiency of cement manufacturing.
Researchers at the University of Florida have developed a high-temperature plasma arc reactor capable of producing the main ingredient of portland cement, clinker, in a highly controlled environment. This reactor avoids the clinker contamination possible with rotary kilns, enables use of recycled waste byproducts in cement manufacturing, and has a less harmful impact on the environment.
A high-temperature plasma arc reactor for cement clinker production that reduces the carbon footprint of cement manufacturing
This reactor aims to optimize and refine cement clinker production by employing high temperatures and a controlled environment. The reactor utilizes a plasma torch to perform the thermal treatment and can fully automate temperature up to 3,000 degrees Celsius, which is twice the temperature produced by a rotary kiln. It also generates the heat without traditional fuel sources to eliminate fuel-borne C02 emissions. After manufacturing clinker, a quantitative X-ray diffraction uses a Rietveld refinement technique to analyze its mineralogical compositions for optimal cement phases.
This manufacturing process takes municipal solid waste bottom ash to produce autoclaved aerated concrete (AAC) sustainably and efficiently. ACC is a lightweight, precast, ecofriendly, and thermally insulated building material. In 2023, the autoclaved aerated concrete (AAC) market size was estimated at USD 15.50 billion and is expected to grow at a compound annual growth rate (CAGR) of 6.0% between 2024 and 2030. The growth of the AAC market is driven by the increasing demand for sustainable and energy-efficient building materials. The market value is in the building and construction industry, in addition, it offers sustainability value in the waste-to-energy industry.
Florida has the most MSWI facilities of any state in the U.S., with most plants commissioned since the early 1990s. These facilities represent 15 to 25% of MSW waste management in Florida, in areas with higher populations. This results in the production of approximately 1 million tons per year of ash residue across 12 facilities in Florida. It is important to identify ways to mitigate the negative health and environmental effects of bottom ash. Currently, the only AAC manufacturing facility using bottom ash in the United States is in Florida.
Traditional AAC production uses aluminum powder as its major aerating component. However, it must be imported from other countries, such as Mexico and Europe, incurring significant costs and reducing the viability of the AAC production. The demand for AAC in the U.S. is outpacing supply and production capacity. However, this technology provides an alternative for aluminum powder obtained from bottom ash following waste incineration.
Researchers at the University of Florida researchers employed bottom ash from municipal waste incineration to produce autoclaved aerated concrete. This provides an alternative source for aluminum powder, helping produce more sustainableand thermally efficient AAC in the United States. It also eliminates the need and cost of importing aluminum powder for AAC production. In addition, it repurposes bottom ash from waste incineration that would otherwise be landfilled, converting waste into a beneficial construction material. Thus, supporting environmental sustainability by finding productive uses for waste byproducts.
Produces autoclaved aerated concrete (AAC) using bottom ash from municipal solid waste incineration as an aerating agent, replacing imported aluminum powder
This autoclaved aerated concrete production offers a sustainable option in the building and construction industry. It uses bottom ash, containing aluminum byproduct, from municipal waste as an aerating agent. This enables aeration in the AAC while eliminating the need to import aluminum and overall reducing the cost of production.
This virtual rotary kiln models the Portland cement manufacturing process and calculates the physical and chemical properties of final concrete materials. The global cement market will exceed $460 billion by 2026 . Rotary kilns are the core for cement manufacturing plants in Portland cement production. Producers increasingly value environmental and energy efficiency in addition to productivity. Regular chemical and physical tests in a lab throughout production can fine-tune cement properties and minimize energy costs, but their implementation on a large scale can be costly and impractical. Likewise, computational modeling can help cement plants optimize energy usage and material mixtures, but the numerous operational parameters make this difficult with available modeling systems.
Researchers at the University of Florida have developed a computational framework that intelligently simulates rotary kiln operation in a virtual cement plant. The software serves as a quantitative optimization tool that calculates the properties of the final Portland cement, removing the need for lab tests and helping plants optimize material mixtures and production ensuring competitive performance of the materials.
Virtual Portland cement plant and testing software that optimizes production for users’ efficiency demands
This virtual cement plant integrates the Virtual Cement and Concrete Testing Laboratory (VCCTL) modeling system into a broader program able to optimize multiple desired concrete characteristics. The one-dimensional software simulates clinkering reactions within a rotary kiln based on operating conditions, kiln geometry, and other relevant user-defined inputs, and determines the thermal, mechanical and transport properties of the resulting cement. Algorithms adjust kiln-operating parameters to reduce material costs, energy consumption, and greenhouse gas emissions without hampering cement performance.
This filtering and curing treatment of waste to energy bottom ash results in a beneficial composite that can be mixed with cement to form environmentally safe concrete. Waste to energy bottom ash or incinerator ash is a portion of the non-combustible residue that remains after waste combustion. Municipal waste combustion generates 7-8 million tons of waste in the United States annually and, because it has the potential to leach concentrations of heavy metals, it currently requires disposal in secure landfills. The construction, permitting, compliance and operating costs of a landfill are significant; recycling bottom ash for beneficial use instead of storing it in a landfill would be a significant cost savings for ash generators. Researchers at the University of Florida have developed a filtering and curing treatment that immobilizes contaminants in the bottom ash and creates a properly graded and usable aggregate product for use in asphalt and concrete or as a roadway base.
Immobilizes contaminants from waste to energy bottom ash allowing use as a construction aggregate
Bottom ash from municipal waste is processed through physical processes to use as an aggregate for a road base, or in Portland cement concrete and hot mix asphalt. The bottom ash moves through gradation screenings to remove metals, elements, alloys and other contaminants. The ash is then cured by selective exposure to water and atmospheric CO2, effectively lowering the pH of the ash and creating an environment that washes heavy metals and trace elements from the ash. The resulting composite has few negative health and environmental effects while maintaining similar structural properties to alternative composites.