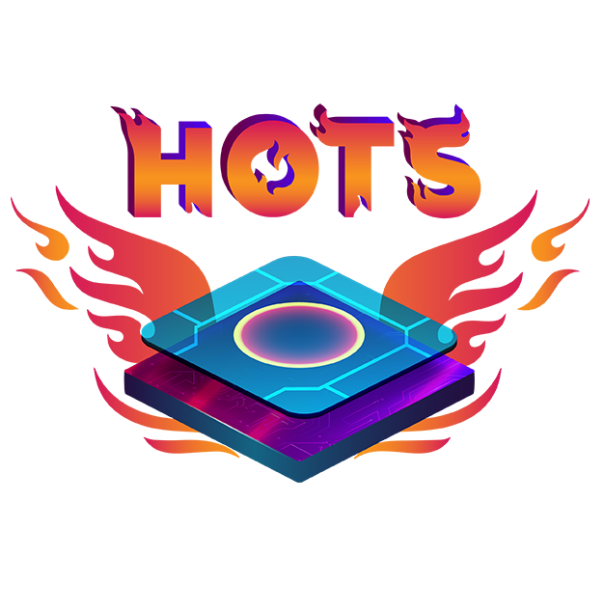
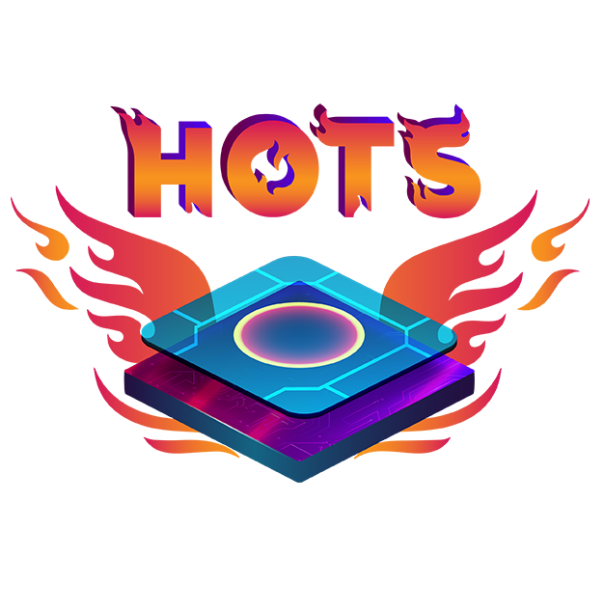
Research Terms
Mechanical Engineering Aerospace Engineering
This micro-electromechanical system or MEMS-based device can measure wall shear stress vectors in 3D aerodynamic flow fields in both controlled environments and field applications. Aviation test equipment is designed to measure wall stress, which is essential to understand and solve aerodynamic drag issues. The global aviation test equipment market is projected to reach a value of over $7 billion by 2020. Only indirect methods, such as hotwires or particle image velocimetry (PIV) field visualization, are available for measuring wall shear stress. These methods require highly controlled testing environments and rely on inferred relations to produce a measurement.
Researchers at the University of Florida have developed a MEMS-based device that is capable of making direct, real-time wall shear stress measurements without secondary measurements or models for validation.
MEMS-based device for measuring wall shear stress vectors in both controlled environments and field applications
This MEMS-based device is made of three components: the floating element, serpentine tethers, and capacitive comb fingers. The floating element allows the device to withstand prolonged exposure to various turbulent fluid fields without encapsulation, while the serpentine tethers allow the device to detect wall shear stress in two directions. The floating element is chemically etched into the silicon wafer so the overall device presents a flat surface to the fluid flow. Structures that protrude into the fluid flow field can corrupt the quality of any measured wall shear stress vectors. This device design can be used to test within controlled environments, such as aerodynamic testing facilities, as well as in field applications, such as airplanes or drones. Thus, assumptions regarding the testing environment are not required to obtain force measurements, nor are secondary measurements or models required for validation.
This improved packaging design protects and optimizes microphone sensors that are used in and around airplanes to help locate and reduce excessive aviation noise, an environmental and human health hazard. Passenger travel in airplanes is expected to increase from 732 million to 1.2 billion by 2032, and the comfort and safety of these passengers and their pilots, as well as the communities surrounding commercial airports, are vital to the continued progress of commercial flight. Widely-used noise detection technologies sacrifice durability and sensitivity for low production costs. Unfortunately, no available cost-effective aeroacoustics instrumentation solutions simultaneously protect microphone sensors and maintain superior sensitivity. Researchers at the University of Florida have developed a superior instrumentation packaging design that decreases production costs without sacrificing instrument sensitivity. This allows for more accurate capture of noise information by the sensor by avoiding the need for a protective encapsulant that dampens differential airflow measurement by the instrument’s sensing processes and makes the diaphragm a direct part of the sensing side of the device, closer to the surface on which the measurement is desired. Additionally, the developed packaging design creates an overall flush front surface of the microphone package, minimizing the impact of the sensor on the measurement. This transformative change is part of a microfabrication system that allows for mass production of these superior sensors at a lower cost than available instrumentation with protective encapsulants.
Sensor packaging for highly accurate aeroacoustics measurement
This packaging design achieves high aeroacoustics instrumentation sensitivity through a microfabrication method that uses backside wire bonds. The sensor is microfabricated on a silicon-on-insulator wafer using through-silicon-vias, then enclosed in a shim cap and attached to a mounting substrate. This design allows the sensor surface to be a direct part of the exposed side of the sensor package – a “flush mount.” The resulting elimination of raised edges on the device eliminates their impact on airflow measurement by a particular sensor and surrounding sensors in an aircraft fuselage array installation. Additionally, microfabrication of the sensor minimalizes cost, allowing greater sensory density in array installations and increasing resolution capabilities for aircraft pressure maps.
This smaller, more sensitive multi-hole probe pressure sensor integrates MEMS-based optical fibers for quicker, more accurate air pressure measurements. Multi-hole probes are flow measurement tools designed to take point measurements at the probe tips when immersed in a fluid flow field. Available multi-hole probes incorporate long pneumatic tubes connecting the probe tip holes to the transducers, resulting in long response time or settling times, also known as pneumatic lag. Pneumatic lag leads to inaccurate and delayed results, increasing experimental analysis turnaround and hindering the detection of high-frequency pressure perturbations. Miniaturization of multi-hole probes is key for improving measurement accuracy and providing high spatial resolution. To date, embedding multiple pressure sensors at the probe tip while maintaining a compact size to minimize pneumatic lag has been challenging.
Researchers at the University of Florida have developed a 5-hole probe pressure sensor integrating MEMS-based single-mode optical fibers into the probe tip to eliminate pneumatic tubing. Enabling at-tip pressure measurements renders merits of fast response and miniaturization and increases sensitivity in air-pressure monitoring on aircraft.
5-hole, multi-hole probe pressure sensor integrating an optical sensor array for faster, more precise monitoring of air pressure changes on the body of an aircraft
This MEMS-based 5-hole probe pressure sensor comprises a probe tip with multiple holes on the top surface, each hole connecting to a tube conveying fluid from the measurement environment to pressure transducers operating through optical lever-based techniques. The pressurized fluid in the probe tip applies force to a diaphragm within the probe, leading to changes in its position as a response to different pressures. Upon application of a light source, the diaphragm reflects light in different patterns depending on the positioning of the diaphragm. The light pattern data are collected and analyzed using a photodiode to determine the environmental pressure acting on the different holes of the probe. The incorporation of fiber-optic lever intensity modulation eliminates the need for traditional pneumatic tubing systems within the probe, enabling at-tip pressure measurements and faster response. This 5-hole probe provides improved laboratory applications, such as boosted wind tunnel test productivity, and field applications on airplanes and UAVs for real-time flight monitoring and feedback control.
This device uses sensors to accurately and quickly process wall shear-stress in applications for the aircraft industry. The measurement of skin friction drag is vitally important to the aircraft industry, and skin friction drag causes an estimated 50 percent of the total vehicle drag for a typical transport aircraft. The macro-scale measurement systems that are widely in use cannot sufficiently meet the demands for directly obtaining accurate shear stress data. And while optical-MEMS-based laser-Doppler anemometers have shown promise, they lack the ability to generate small measurement volumes in high numbers.
Researchers at the University of Florida have created a floating-element shear stress sensor that allows direct, high temperature measurements of skin friction. This device allows for quick, accurate quantitative measurements and covers high-ranging temperatures, providing advantages in efficiency, applicability, and functionality when compared to available shear-stress sensing systems.
A sensing system that accurately and quickly processes wall shear-stress in aircraft industry applications
This sensing system uses floating-element shear stress sensors that enable the direct, high temperature measurement of skin friction based on geometric and/or interferometric optical techniques. Since they use materials able to transmit, absorb, or reflect optical signals, the sensors maintain functionality at higher temperatures. Additionally, the use of high-temperature materials such as sapphire allows use of the sensing system at a distance for various temperature-sensitive electronics.
This low-maintenance, passive wireless sensor uses a microelectromechanical system (MEMS) and radiofrequency waves to measure static and dynamic pressures accurately for applications in harsh environments, such as gas turbines. Many industries require pressure sensors that maintain accurate operation even when subject to severe environmental hazards. However, these harsh environments often damage the pressure sensors, which then demand regular maintenance. Notably, this problem occurs in high-temperature gas turbines, which are powered by the hot gases produced by burning fuel. Pressure fluctuations in the air flow across the turbine blades and vanes cause high cycle fatigue, the primary source of component failure in gas turbines. A sensor that can properly measure pressure in this harsh environment would better detect local pressure fluctuations and aid in preventing high cycle fatigue. Although optical sensors successfully measure pressure in harsh environments, they are quite expensive, use fragile filaments, and are difficult to package.
Researchers at the University of Florida have developed a sensor that functions wirelessly and passively to detect both static and dynamic pressure in high-temperature environments. The sensor can apply to a variety of applications requiring pressure measurement in the presence of high temperatures, such as gas turbines, jet engines, or nuclear power generators.
Passive wireless pressure sensor that maintains operation in extreme environments
This microelectromechanical system (MEMS) sensor is both passive, meaning no internal energy sources such as batteries are required, and wireless. A diaphragm on the sensor deflects either downward or upward based on the surrounding pressure. The sensor attaches to an area of interest and uses radio frequency electromagnetic signals to communicate the current pressure of the environment with a computer-based simulation that analyzes the signals to determine the area’s fluid flow. This sensor can determine both static and dynamic pressures and also can detect uncontrolled fluid flow early, preventing any damage to engines or other equipment.
Mechanical and Aerospace Engineering 227 BEN PO BOX 116200 GAINESVILLE, FL 32611